tig weld gap sheet metal Sharing my go to method for TIG welding up a gap. This is one of many ways to do it but I often end up with a weld that looks just as good as a perfect joint. If you are a SMART sheet metal member who is out of work and willing to travel to the jurisdiction of other local unions to work, PLEASE CONTACT YOUR LOCAL UNION OFFICE. Frequently Asked Questions for Travelers. We have developed a list of frequently asked questions to assist members when exploring their options of traveling for work.
0 · welding thin to thick metal
1 · welding stainless steel sheet metal
2 · welding sheet metal without warping
3 · welding 14 gauge sheet metal
4 · tig welding stainless sheet metal
5 · tig welding automotive sheet metal
6 · mig welding galvanized sheet metal
7 · 18 gauge weldable sheet metal
At Trayco we fabricate all types of custom steel Trays at highly competitive prices. We also supply and carry a large range of Hayman Reese products at our premises in Launceston. Call us .
welding thin to thick metal
Sharing my go to method for TIG welding up a gap. This is one of many ways to do it but I often end up with a weld that looks just as good as a perfect joint. Preventing burn-through and warping when welding sheet metal is all about controlling the heat. Choose the right welding process and filler metal, and follow these . A new TIG welder asks, “How do I know when my fitup is so bad I need to cut a patch rather than fill a gap when TIG welding?” When you’re welding a butt joint, you want .
In this article, I am going to explain the fundamental ways of how to weld sheet metal that even professionals can follow. I have also put together a list of best welders for .TIG (Tungsten Inert Gas) welding excels at joining thin sheet metal. It provides superior control, minimal distortion, and clean, strong welds. By using a non-consumable tungsten electrode and inert gas shielding, TIG allows for precise .
black box distribution skateboards
What metal are you welding? Aluminum. Deoxidized Copper. Magnesium. Stainless Steel/Steel. Browse suggested weld parameter settings for TIG Welding. Thin sheet metals are highly susceptible to warping and burn-through if the welding settings are not properly dialed in. Achieving the perfect balance of amperage, voltage, tungsten size, and gas flow rate is the key to .
When you’re TIG welding sheet metal, you don’t want there to be any gap. You want your two pieces to be flush, and it’s a good idea to have it clamped at regular intervals while you do the tacks so that one side can’t lift or . Did you know that TIG welding is the best option for sheet metal? The biggest problem any welder is going to face when it comes to sheet metal is the heat in. Anybody have any advice on tig welding 18 gauge steel? I can seem to do 16 gauge alright way down at 9 amps but 18 gauge is just blow through from the moment I pull the trigger. . It's up to you to manipulate sheet .
When working with sheet metal, it’s important to consider the material’s thickness and composition. Thin sheet metals are highly susceptible to warping and burn-through if the welding settings are not properly dialed in. . For thin sheet metal welding it can be 30 ampere while for thicker (e.g. 1/8” square groove weld)- it can go up to 220 ampere for example. GMAW-S gives low heat and makes it easy to use in all positions on sheet metal, low . #welddotcomThis video was by special request from a viewer (arcstreams). He asked that we demonstrate some tips for welding mild steel sheet metal and some o. Kind of a followup to my "How To TIG Any Gap" video. This one uses the same technique but on this exact use case. Thin steel boxed tubing. This would also wo.
Where possible try and get the two pieces of sheet to be as level with one another as possible. Reason, if you have say 1/3 of the thickness standing higher than the other then once you have welded it when it cones to grinding back to blend in you will need to take away some of that metal that is standing proud and will thin the 1.0 mm to aprox 0.7 mm making for a thin .
Did you know that TIG welding is the best option for sheet metal? The biggest problem any welder is going to face when it comes to sheet metal is the heat in. 8 TIG Welding. 8.1 Considerations for TIG welding; 9 Sheet Metal Part Design for Manufacturing Tip. 9.1 CORNERS AND WELDING; 10 Sheet Metal Fabrication Welding FAQ. 10.0.1 What are the key welding methods used by fabricators? 10.0.2 What is the difference between spot welding and tack welding?Mastering TIG Welding Techniques for Sheet Metal. TIG welding sheet metal demands precision and skill. Let’s explore the techniques that will elevate your welding game. Key Principles of TIG Welding Sheet Metal. Success in TIG welding sheet metal hinges on several core principles: Maintain a short arc length, typically 1/8 inch or less.Most of the light gauge sheet metal work will require the use of .023- or .24- inch while if you have a sheet metal having a gauge of more than 18-gauge then a .030-inch wire would be the most ideal. A ER70S-6 wire would be most ideal for welding mild steel.
How to Weld Auto Body Sheet Metal With a TIG Welder. The best two electrodes for welding auto body sheet metal are either ceriated tungsten or thoriated tungsten. Ditch a 1/8-inch tungsten electrode for something much smaller, like 1/16-inch tungsten — it will give you a lot more control over the whole process, and it is more forgiving in .In this video I show how to Mig weld any gap. This process is useful when you get your cuts off a little bit or your angles are off a little. This happens to. You are talking about sheet metal so penetration and strength won't be an issue. Heat and warping are a bigger factor to worry about. . The metal in the weld area doesn't ''knit or flow'' together as it does in a gas or tig weld (yet another reason I detest squirtgun welds for sheetmetal repair) This can lead to pin holes in the weld and .
The gap between the sheet metal edges should be as small as possible, ideally zero, or up to 0.5mm at most. A larger gap can cause the arc to wander, the filler to drip, or the weld to be weak. . TIG welding sheet metal is a skill that requires practice and patience, but it can produce excellent results if done correctly. By following the .1/16 filler on 1/16 sheet metal doesn't work well. The amount of heat required to melt the sheet is vasty different from the heat for both sheet and filler. 16 gauge sheet metal is much, much easier with .040 filler. The heat range is better. If you can't get some tig wire, you can uncoil a spool of .045 might wire.
welding stainless steel sheet metal
welding sheet metal without warping
Butt welding sheet metal is a fundamental welding technique that involves joining two metal sheets end-to-end. This process creates a strong and durable weld, . based on the characteristics of the metal being welded. For .
Sheet metal thickness suitable for welding typically ranges up to 1/4 inch using MIG or TIG welding, with TIG preferred for finer work on thinner metals. Which welding is best for thick metal? Stick welding or Flux-Cored Arc . When your tig welding sheet metal, you don't want there to be any gaps. . Instead, you weld straight over the top of them to avoid leaving a gap so the flatter they are to start the better. Once you've . If this was your first ever sheet metal butt weld I'd try more practice first. Then I'd discover all the cutting tricks and tips. Because if its setup and done right Stevie Wonder and Ray Charles can cut a perfectly matched line on panel and patch. . You need to make sure your panel gap is correct. If you are not TIG or Oxy welding then you . Today we're going to demonstrate how to butt weld sheet metal using a Lincoln Electric mig welder. Like anything, there's a right way and a wrong way to butt.
Find below the MIG Welding Sheet Metal Settings Chart which displays the recommended settings for welding different gauge thicknesses of sheet metal. To ensure optimal results, select the appropriate gauge thickness and refer to the corresponding joint gap, wire diameter, amperage, and voltage setting for your weld. A small diameter tungsten electrode in TIG welding with small diameter filler rod is the perfect friend when you weld thin stainless steel sheet metal or tubing. Secondly, choose the correct welding parameters- Welding current (Amperage). 40 to 60 ampere is the right when welding thin stainless steel.
Welding nearly always causes some distortion: the metal in and around the weld shrinks as it cools, and this shrinking often upsets the shape of the metal. Sheet metal is particularly sensitive to this type of distortion (often called warping) but there are ways to mitigate this characteristic, which we will detail here. Due to its high-quality weld seam and excellent arc stability, narrow gap Tungsten Inert Gas (TIG) welding has become a critical technology for welding thick metal plates. However, this technology has the problem of insufficient sidewalls penetration, which has a significant impact on the performance of the components. This study provides a comprehensive overview .
Now, I have not worked with sheet metal, but spit-balling - could you make it a bit longer in that direction, snip the corner, bend it so it is rounded like the other corners, then fold the flaps over each other and spot weld/rivet/glue depending on what you need. . As you have it now, that gap looks a bit big to weld nicely, with TIG anyway . TIG welding sheet metal can be challenging because it requires a low heat input and a high travel speed to prevent warping or burn-through. Here are some steps to follow when TIG welding sheet metal: . Leave a gap of about 2 mm (0.08 inches) between them. Clamp them together firmly with a backing bar or a backing gas to support the weld pool .
11. Sheet Metal Tips. As mentioned in the introduction, sheet metal work is a different animal than steel beams. Any of the above practices can be useful in mitigating distortion in sheet metal, but there are additional practices that can come into play and perhaps save the day. These include: Water-Cooled Jig
billet cnc machining
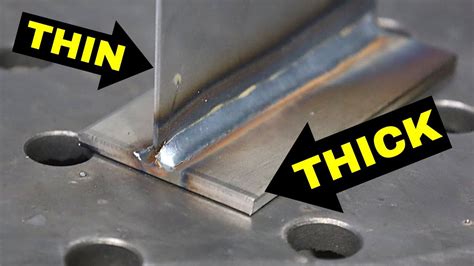
Metal Panels Inc. manufactures a wide selection of custom trim up to 21 ft. in length for standing seam and through-fastener metal panel roofing and buildings. Our trim is typically a heavier gauge than offered elsewhere, to resist warps and dings, and increase installed durability.
tig weld gap sheet metal|18 gauge weldable sheet metal