punching in sheet metal Sheet metal punching stands as a cornerstone of precision sheet metal fabrication, offering unparalleled versatility, precision, and efficiency in creating a diverse range of metal components. As the industry continues to . Learn why MIG, pulsed MIG, TIG and pulsed TIG are the ideal choices when welding sheet metal. When welding thin metal, the main objective is to avoid warping, burn-through and excessive heat-affected zones while still .
0 · trimming operation in sheet metal
1 · sheet metal punching die
2 · punching operation in sheet metal
3 · perforating operation in sheet metal
4 · lancing operation in sheet metal
5 · difference between punching and blanking
6 · difference between piercing and punching
7 · blanking operation in sheet metal
Custom metal stairs, commonly fabricated from steel or aluminum. Design, build & install. Shafts, catwalks, specialty platform, small/large roof access.
Punching blanking and piercing are sheet metal shearing operations to modify existing blank. Similar machines but different punch and .
Sheet metal punching is a cost-effective and accurate process for creating holes and shapes in sheet metal components. By following a guide, implementing quality control, addressing challenges, and ensuring safety, . Sheet metal punching uses a punch press to cut specific shapes from sheet metal, creating predetermined forms. The removed piece, called a slug, is typically discarded as . Sheet metal punching stands as a cornerstone of precision sheet metal fabrication, offering unparalleled versatility, precision, and efficiency in creating a diverse range of metal components. As the industry continues to .
Punching is an operation that involves punching holes or other more complex shapes to remove material from metal sheets. The removed material ends up as scrap which is the complete opposite of blanking wherein .
A: Punching in sheet metal is a fabrication technique that involves creating holes or shapes in sheet metal by forcing a tool called a punch through the material and into a die. Q: What factors affect the sheet metal punching .This level of automation facilitates high-speed and versatile perforation of metal sheets. NCT Punching Advantages . High-Speed Perforation: NCT punching excels in high-speed perforation, making it well-suited for mass production scenarios where efficiency is paramount. Sheet metal punching is a relatively simple process, but it is important to follow safety guidelines and use the correct techniques to ensure a safe and successful operation. Proper tooling prep, precise part fixturing, and process monitoring helps achieve consistently accurate punched components.
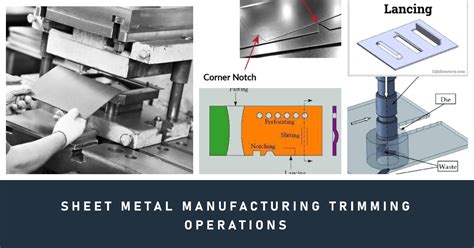
Given: It is desired to punch of hole in a sheet of metal, with the metal having a thickness of t. The desired hole is square with dimensions of b x b, as shown below. The punching force is given by P. Find: Determine the shear stress in the plate as a result of the punching force P. For this problem, use the following parameters: t=0.1 in, b .NEWTRY 8mm Pneumatic Hole Puncher Air Metal Hole Punch Tool Industrial Sheet Metal Punching Gun Heavy Duty Metal Hole Flange Opener for Doors & Windows, Factory, Office and Home. 3.8 out of 5 stars. 37. 9.00 $ 129. 00. 5% off coupon applied Save 5% with coupon. FREE delivery Mon, Nov 18 .
Metal Punching Capacity: Capable of processing X12’ x Y4’ sheets; Maximum sheet thickness: .250” Press capacity: 33 ton; Punching accuracy: ± .005” AS9100D Certified Metal Punching. Hallmark Metals is a AS9100D certified business which specializes in precision metal punching.
The CNC punching machine and the CNC turret punching machine can produce a sheared crack joint, maintain a balanced blanking force, ensure good punching quality, and extend the service life of the mold. It is recommended to refer to the punch and die clearance table (as shown in Table 1) for optimal results. Table 1. Punch & Clearance Chart . Sheet metal punching uses a punch press to cut specific shapes from sheet metal, creating predetermined forms. The removed piece, called a slug, is typically discarded as scrap metal. This method excels at quickly producing repeatable and consistent parts, making it ideal for high-volume production and mass manufacturing processes. . What are the Advantages of Sheet Metal Punching? It has several advantages in metal fabrication, from its precision and speed to cost-effectiveness and versatility. Here are six key advantages of sheet metal punching; 1. Precision and Accuracy. The CNC sheet metal punching machines are capable of very high precision and accuracy. The 3:1 Rule for Sheet Metal Punching. The 3:1 rule states that when designing a formed feature in a precision sheet metal part, the feature's height should be no more than 3x the material thickness above the material surface.
Sheet metal punching, or subtractive manufacturing, creates holes, slots, or shapes by applying a mechanical punch through sheet metal. The force, usually made of hardened tool steel and pierces through the metal, removes the piece, leaving a precise shape on the sheet.
trimming operation in sheet metal
You can mold the geometry of a sheet metal part by referencing a punch form model, a die form model, a sketch, a solid body, or a quilt. When assembling a punch form or a die form reference, make sure that the driving sides of the reference model and of the sheet metal part match. You can pattern punch, die, sketch, and quilt form features and .
How Sheet Metal Punching and Notching Operation Compare. The two processes compare in the following ways; Variable: Sheet metal punching: Notching operation: Surface of operation : It only takes place within . P.S: If you want to calculate hydraulic press tonnage, you can use our hydraulic press tonnage calculator.. Related calculator: V & U-shaped Bend Force Calculator Press Tonnage Calculation Formula. If you need to punch . Sheet metal punching, also known as metal stamping, involves creating holes, forms, or other features on a metal surface using a punch and die. It is a crucial process in the fabrication industry, enabling efficient production .
Tool for punching shapes out of sheet metal? My wife has an idea for some new crafts and she wants to be able to quickly cut shapes out of sheet metal (stars, hearts, clovers, other lucky charms marshmallows) All I have to offer her for use are metal snips and a round metal punch. Neither of which she seems thrilled with the prospect of.
Sheet metal punching defines a slitting process, in which a punching machine or press separates a sheet of metal by striking it. Punching is a mechanic process in which a sheet is perforated by a single stroke of the machine. Individual hit can produce shapes such as circular holes or outer contours. Due to the way sheets are cut, a process is .Sheet metal punching is the most efficient way to produce precision fabricated metal products with many holes. For over 60 years, Classic Sheet Metal has been a top choice for sheet metal punching in Chicago and in the United States. Our sheet metal punching machine can also form countersinks, embossments, extrusions, and louvers.Sheet Metal Turret Punching. A turret punch (or turret press) is a type of punch press that is used for making extremely accurate holes and features in sheet metal. These machines are excellent for mass production and are often used to build individual parts for different products. Midland Metal Products offers a wide range of turret punching .Sheet metal punching tools are traditionally manually operated, but newer technology allows for automated and computer controlled punches that can create more intricate designs and mass produced punches. Punches can range in size, shape, quantity, and spacing. Although the first thing you might think of is a round hole, sheet metal punches can .
Punch force is the amount of force required to create a hole or cut in a sheet metal workpiece. It is a crucial parameter in sheet metal fabrication processes, particularly in punching operations. The punch force depends on several factors, including the material properties, thickness of the sheet, and the shape and size of the desired hole or cut. The main difference between blanking and punching is that in blanking, the final product is removed out of the larger metal sheet, and the remaining material is discarded as scrap, whereas in punching, the material removed out is discarded, and the final product is the remaining material.. Blanking and punching are two metal production methods. Moreover, they .Metal Punching, Cutting and Forming Services. Need metal punching, cutting or forming services? You’ve come to the right place. The can-do team at Swanson Sheet Metal takes pride in delivering high quality results quickly, effectively and efficiently. Whether you’re located in our neighborhood in North Carolina or across the country, our .
This case study examines the use of sheet metal punching in electrical enclosure manufacturing. We will cover the benefits, processes, and important considerations of this technique. Through a real-life case study, we will highlight the benefits of leveraging this method for electrical enclosure fabrication. . Metal sheet punching machines have revolutionized the metal fabrication industry by automating the process of creating precision holes and shapes in metal sheets. This cutting-edge technology has transformed manufacturing processes, providing numerous benefits in terms of efficiency, precision, and versatility. Enhanced Efficiency Reduced Labor Requirements: .
sheet metal punching die
Best Metal Fabricators in Kent, WA - AC Custom Metal Work, Allied Steel Fabricators, Specialty Metals, Metal Magician, AAA Welding Company, Metal Supermarkets, J & R Metalcraft Fabricators, Exor Ironworks, Willow Welding, American Manufacturing and Engineering
punching in sheet metal|difference between punching and blanking