double hem sheet metal Sheet metal hemming is a unique technique that involves folding the edge of sheet metal back on itself to create a double thickness. This process adds durability and strength to the part but eliminates sharp edges. CONVENIENT SETUP: Our exterior weatherproof electrical box comes with closure plugs and reducer bushings for your convenience. It also includes an optional rain collar for weatherproof fans. STURDY SUPPORT: You get a solid mount for fans up to .
0 · sheet metal hemming machine
1 · open hem sheet metal
2 · open hem meaning
3 · hemming process
4 · hemming in sheet metal
5 · hemming die
6 · hemmed edges
7 · doubling a sheet metal hem
Safeguard outdoor electric wires and cable terminals from dust and low-pressure water jets with an IP55 junction box. IP55 junction boxes are ideal for low-level weather damage protection. Find waterproof socket covers to keep electricals safe from dust and water jets.
The four most common types of sheet metal hems used by Approved Sheet Metal are closed hem, teardrop hem, open hem, and rolled .A two stage hemming die works by using a deep channeled die and an acute sword punch. The first bend uses the channel as a v opening to air form the bend. In the second stage the punch slides into the channel as the punch is closed .The DOUBLE-HEM EDGE (fig. 2-55) is used when added strength is needed and when a smooth edge is required inside as well as outside. The allowance for the double-hem edge is twice the .Sheet metal hemming is a unique technique that involves folding the edge of sheet metal back on itself to create a double thickness. This process adds durability and strength to the part but eliminates sharp edges.
Hemming in sheet metal operations refers to the bending of a sheet metal edge onto itself. It is very similar to edge stitching in clothes. Similar to how an edge stitch strengthens the edge and makes it more durable, a hem . Sheet metal hemming is a manufacturing process that folds metal edges to reinforce strength and safety. It reduces sharpness and enhances aesthetics, often used in .
Sheet metal hemming is a metal-forming technology that involves rolling or folding sheet metal edges over and onto itself. You have to fold over the edges of sheet metal to create an area with two layers. A hem is a single, 180-degree bend. Some hems are closed—basically a zero inside bend radius. If the hem has a radius greater than zero, it resembles a U in cross section. Unlike the U-channels discussed in .
ceiling fan in standard electrical box
Two hemmed sheet metals will form a strong joint that can help create a durable assembly for any product you build. The cut sheet metal components will often have rough edges, which pose a safety risk when you handle them. Applying .
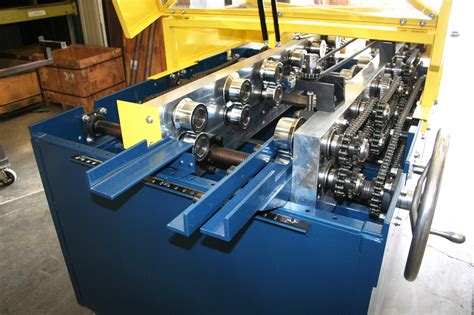
The four most common types of sheet metal hems used by Approved Sheet Metal are closed hem, teardrop hem, open hem, and rolled hem. What are the material limitations for closed hems? Closed hems work best with material thicknesses of .040"-.125".A two stage hemming die works by using a deep channeled die and an acute sword punch. The first bend uses the channel as a v opening to air form the bend. In the second stage the punch slides into the channel as the punch is closed and the edge of .The DOUBLE-HEM EDGE (fig. 2-55) is used when added strength is needed and when a smooth edge is required inside as well as outside. The allowance for the double-hem edge is twice the width of the hem.
Sheet metal hemming is a unique technique that involves folding the edge of sheet metal back on itself to create a double thickness. This process adds durability and strength to the part but eliminates sharp edges.
Because they are so simple to create—the sheet metal is flattened upon itself—closed hems are the most common kind of hem. To prevent breaking, the flat length of the hem must be at least four times the thickness of the material. Hemming in sheet metal operations refers to the bending of a sheet metal edge onto itself. It is very similar to edge stitching in clothes. Similar to how an edge stitch strengthens the edge and makes it more durable, a hem imparts strength to the . Sheet metal hemming is a manufacturing process that folds metal edges to reinforce strength and safety. It reduces sharpness and enhances aesthetics, often used in automotive, aerospace, and consumer goods industries.
Sheet metal hemming is a metal-forming technology that involves rolling or folding sheet metal edges over and onto itself. You have to fold over the edges of sheet metal to create an area with two layers. A hem is a single, 180-degree bend. Some hems are closed—basically a zero inside bend radius. If the hem has a radius greater than zero, it resembles a U in cross section. Unlike the U-channels discussed in Part III, the hem has only one bend instead of two. If no flat section to the hem is evident, it is simply an edge bead.Two hemmed sheet metals will form a strong joint that can help create a durable assembly for any product you build. The cut sheet metal components will often have rough edges, which pose a safety risk when you handle them. Applying a hemming procedure can eliminate the rough edges on these sheet metals.
The four most common types of sheet metal hems used by Approved Sheet Metal are closed hem, teardrop hem, open hem, and rolled hem. What are the material limitations for closed hems? Closed hems work best with material thicknesses of .040"-.125".
A two stage hemming die works by using a deep channeled die and an acute sword punch. The first bend uses the channel as a v opening to air form the bend. In the second stage the punch slides into the channel as the punch is closed and the edge of .The DOUBLE-HEM EDGE (fig. 2-55) is used when added strength is needed and when a smooth edge is required inside as well as outside. The allowance for the double-hem edge is twice the width of the hem.
Sheet metal hemming is a unique technique that involves folding the edge of sheet metal back on itself to create a double thickness. This process adds durability and strength to the part but eliminates sharp edges.Because they are so simple to create—the sheet metal is flattened upon itself—closed hems are the most common kind of hem. To prevent breaking, the flat length of the hem must be at least four times the thickness of the material.
Hemming in sheet metal operations refers to the bending of a sheet metal edge onto itself. It is very similar to edge stitching in clothes. Similar to how an edge stitch strengthens the edge and makes it more durable, a hem imparts strength to the . Sheet metal hemming is a manufacturing process that folds metal edges to reinforce strength and safety. It reduces sharpness and enhances aesthetics, often used in automotive, aerospace, and consumer goods industries.
sheet metal hemming machine
Sheet metal hemming is a metal-forming technology that involves rolling or folding sheet metal edges over and onto itself. You have to fold over the edges of sheet metal to create an area with two layers. A hem is a single, 180-degree bend. Some hems are closed—basically a zero inside bend radius. If the hem has a radius greater than zero, it resembles a U in cross section. Unlike the U-channels discussed in Part III, the hem has only one bend instead of two. If no flat section to the hem is evident, it is simply an edge bead.
ceiling electrical box on bar
open hem sheet metal
open hem meaning
$17.88
double hem sheet metal|hemming in sheet metal