effect of lubrication on sheet metal forming Engine oil 10W-40 was found to be the least favourable lubricant in reducing the coefficient of friction of Grade 5 titanium sheets. The two main tribological mechanisms, i.e., galling and . Struggling to source CNC parts? Explore THECNCSOURCE.COM for easy access to top brands like Renishaw, Blum, Heidenhain, Acu-Rite, Zebra Skimmers and more.
0 · sheet metal forming oil friction
1 · sheet metal forming lubrication
2 · sheet metal forming grease
3 · sheet metal forming friction chart
4 · forming oil for sheet metal
5 · forming lubricant for metal
Welcome to Anebon - your trusted factory partner for high-speed milling of small parts at wholesale prices. We specialize in precision machining services and provide top-notch quality products to our customers. Contact us today and let us help you bring your designs to life!Top Wholesale CNC Slant-Type Bed Lathe Machine Manufacturers: 1. Haas Automation, Inc.- Based in the United States, Haas Automation is one of the world's premier CNC machine .
Engine oil 10W-40 was found to be the least favourable lubricant in reducing the coefficient of friction of Grade 5 titanium sheets. The two main tribological mechanisms, i.e., galling and .
The type of lubrication regime which occurs in a metal forming operation has a strong influence on the frictional conditions as well as on other important factors such as . In this work, the application of a process-integrated lubrication in a deep-drawing process is investigated. Most promising geometries of the lubrication channels and outlet .Friction and lubrication are of vital importance in most metal forming opera tions. Effective lubrication systems result in low friction levels which reduce the
A better understanding of the fundamentals of lubrication in metal forming can lead to more effective lubrication systems and to better process models. Research on lubrication in . In this section, two sheet metal forming processes are used to validate the developed friction model under the boundary lubrication conditions: (1) U-drawing bending and . In the stamping of automotive parts, friction and lubrication play a key role in achieving high quality products. In the development process of new automotive parts, it is therefore crucial to. In order to find the effect of material property and lubricant viscosity on the frictional characteristics of both coated and uncoated metals, a sheet metal friction tester was .
Ensuring adequate lubrication is a key task in the sheet metal forming process. The replacement of commonly used synthetic lubricants in metal forming operations by eco-friendly equivalents.Any metal forming lubricant must reduce friction and wear of the tooling and workpiece and, in the case where high forming temperature is an issue, dissipate heat. However, lubricants also affect and are influenced by numerous other processes within the production chain.Engine oil 10W-40 was found to be the least favourable lubricant in reducing the coefficient of friction of Grade 5 titanium sheets. The two main tribological mechanisms, i.e., galling and ploughing, played the most important role in the friction process on the test sheets.
The type of lubrication regime which occurs in a metal forming operation has a strong influence on the frictional conditions as well as on other important factors such as product surface finish and tooling wear rates. In this work, the application of a process-integrated lubrication in a deep-drawing process is investigated. Most promising geometries of the lubrication channels and outlet openings are first identified by means of numerical simulation at the .Friction and lubrication are of vital importance in most metal forming opera tions. Effective lubrication systems result in low friction levels which reduce the A better understanding of the fundamentals of lubrication in metal forming can lead to more effective lubrication systems and to better process models. Research on lubrication in different regimes and on the modeling of lubrication and friction is reviewed.
In this section, two sheet metal forming processes are used to validate the developed friction model under the boundary lubrication conditions: (1) U-drawing bending and (2) in-line incremental die forming process. The schematics of sheet metal forming processes with relevant dimensions are shown in Fig. 11. In particular, the in-line .
In the stamping of automotive parts, friction and lubrication play a key role in achieving high quality products. In the development process of new automotive parts, it is therefore crucial to. In order to find the effect of material property and lubricant viscosity on the frictional characteristics of both coated and uncoated metals, a sheet metal friction tester was designed and tensile test, surface roughness test, and friction test were performed with several kinds of drawing oils. Ensuring adequate lubrication is a key task in the sheet metal forming process. The replacement of commonly used synthetic lubricants in metal forming operations by eco-friendly equivalents.
sheet metal forming oil friction
Any metal forming lubricant must reduce friction and wear of the tooling and workpiece and, in the case where high forming temperature is an issue, dissipate heat. However, lubricants also affect and are influenced by numerous other processes within the production chain.Engine oil 10W-40 was found to be the least favourable lubricant in reducing the coefficient of friction of Grade 5 titanium sheets. The two main tribological mechanisms, i.e., galling and ploughing, played the most important role in the friction process on the test sheets.
The type of lubrication regime which occurs in a metal forming operation has a strong influence on the frictional conditions as well as on other important factors such as product surface finish and tooling wear rates.
In this work, the application of a process-integrated lubrication in a deep-drawing process is investigated. Most promising geometries of the lubrication channels and outlet openings are first identified by means of numerical simulation at the .Friction and lubrication are of vital importance in most metal forming opera tions. Effective lubrication systems result in low friction levels which reduce the A better understanding of the fundamentals of lubrication in metal forming can lead to more effective lubrication systems and to better process models. Research on lubrication in different regimes and on the modeling of lubrication and friction is reviewed.
In this section, two sheet metal forming processes are used to validate the developed friction model under the boundary lubrication conditions: (1) U-drawing bending and (2) in-line incremental die forming process. The schematics of sheet metal forming processes with relevant dimensions are shown in Fig. 11. In particular, the in-line . In the stamping of automotive parts, friction and lubrication play a key role in achieving high quality products. In the development process of new automotive parts, it is therefore crucial to. In order to find the effect of material property and lubricant viscosity on the frictional characteristics of both coated and uncoated metals, a sheet metal friction tester was designed and tensile test, surface roughness test, and friction test were performed with several kinds of drawing oils.
sheet metal forming lubrication
sheet metal fabrication fort collins co

sheet metal fabrication for electronics manufacturing industry
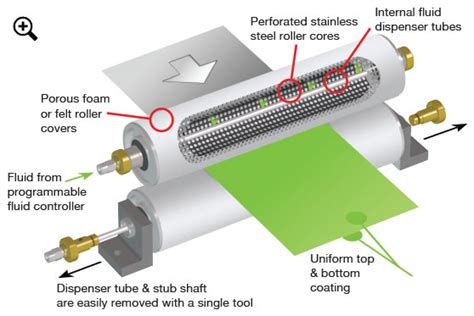
sheet metal forming grease
Router bits are crafted from special and high-quality materials to ensure durability, sharpness, and consistent performance. Carbide-tipped bits are particularly popular due to their outstanding cutting ability and extended lifespan.
effect of lubrication on sheet metal forming|sheet metal forming lubrication